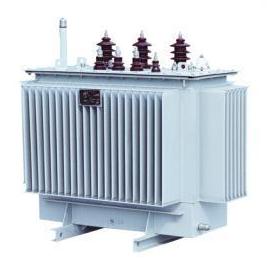
After the power transformer is subjected to a short-circuit shock, a large amount of gas may accumulate in the gas relay. Therefore, after the transformer accident, the gases in the gas relay and the oil power transformer inside the transformer may suffer from a short circuit, and a large amount of gas may accumulate in the gas relay. Gas, so after the transformer accident can take the gas inside the gas relay and test the oil inside the transformer, you can determine the nature of the accident.
Second, attention should be paid to the transformer short-circuit fault handling.
(1) When replacing insulation, ensure the performance of the insulation.
When dealing with the insulation of the replacement should test its performance, and meet the requirements before use. Special attention should be paid to the insulation of the lead frame block. The blocks should be placed in a hot transformer oil of about 80°C for a period of time before installation to ensure the insulation of the blocks.
(2) Transformer insulation test should be carried out 24 hours after the transformer is injected with oil.
Due to the fact that some moisture-proof insulators will remain in the insulating surface after a long time in the hot oil, if the test is performed after the oil is injected, the insulation defect will not be checked. For example, a low-voltage side of a 31.5mVA 110kV transformer was replaced with a bracket wood block of the kv copper row. After the transformer was filled with oil, everything was normal. The insulation resistance of the core, clamps, and ground at the low voltage side of 10kv was reduced to about 1mΩ. After the hood inspection, it was found that the insulation of the 10 kv copper bar is very low. Therefore, the insulation test should be performed more reliably after the transformer is injected with oil for 24 hours.
(3) The core should be attached to the sharp corners.
When loading the iron yoke back, attention should be paid to the sharp angle of the iron core chip, and the insulation between the oil passages should be measured in time. In particular, attention should be paid to the chip sharp angle at the oil passage, and the multi-point grounding of the iron core should be prevented by the chip overlapping. For example, a 220mv 220kv transformer, when replacing the windings on the low-voltage side and returning the iron yoke, did not pay attention to the chip angle when reloading, and did not measure the insulation between the oil passages in time. After installation, the insulation between the oil passages was measured to be 0. The last time it took to find it was due to the shorter corner of the iron core chip.
(4) Replace the winding material with high resistance to short circuit and improve the structure.
The mechanical strength of the transformer winding is mainly determined by the following two aspects: one is the mechanical strength of the winding determined by the structural factors of the winding itself; the other is the support of the inner diameter side of the winding and the axial compression structure of the winding and the pull plate, the clip, etc. The mechanical strength determined by the manufacturing process. At present, most transformer manufacturers use semi-hard copper wires or self-adhesive transposed conductors to increase the ability of the windings to withstand short-circuits. The use of better-quality cardboard tubes or increasing the number of stays increases the ability of the windings to withstand radial forces. And the use of pull plate or spring compression nails to improve the ability of the winding axial force. As the technical department of the power transformer, when signing the technical demonstration prior to the signing of the transformer sales contract and when replacing the transformer windings, the short-circuit capability of the windings should be fully examined and given sufficient attention.
Power transformer gas and oil analysis (5) transformer drying.
Since the transformer generally takes a long time for maintenance after being subjected to a short-circuit shock, two measures can be taken to prevent the transformer from getting wet:
First, the transformer is buckled before the daily work is completed. The vacuum pump is used to vacuum the transformer to remove free water from the surface of the transformer body. When the second day starts, dry nitrogen or dry air is used to relieve the vacuum. The transformer is generally overhauled. The hot oil circulation can be put into operation directly after 24 hours;
The second is to take rainproof measures on the transformer after the daily work is done. After the work is completed, the transformer is dried by the hot oil spray method. This method generally takes 7-10 days.
In addition, after a short-circuit fault in the transformer, in addition to testing the transformer in accordance with the conventional project, the nature of the fault should be determined based on the test results of transformer oil, gas in the gas relay, winding DC resistance, winding capacitance, and winding deformation measurement. And check the deformation of the windings, the displacement and looseness of the iron core and the clamps, and then determine the treatment plan for the transformer and the preventive measures that should be taken. When windings are severely deformed due to transformer short-circuit faults and windings need to be replaced, attention should be paid to the reloading of iron core chips, the drying of all insulation parts, the treatment of transformer oil, and the overall drying of transformers.
Monitor Pole, Steel Monitor Pole, Highway Monitor Pole, Monitor Light Pole
YIXING FUTAO METAL STRUCTURAL UNIT CO.,LTD( YIXING HONGSHENGYUAN ELECTRIC POWER FACILITIES CO.,LTD.) , https://www.chinasteelpole.com