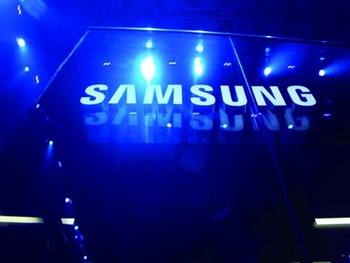
It is reported that Samsung has become the world's largest manufacturer of chips, flat panel displays, mobile phones and televisions, and also has the world's best-selling smartphones, but Samsung is not satisfied with this, and is also preparing to shrink the industry with home appliances and Whirlpool and Electrolux and other industries Leading gap.
Yin Fugen, president of Samsung’s home appliances division, said: “I believe that Samsung will become the world’s largest home appliance manufacturer in 2015 and its sales will reach US$18 billion. We will accelerate the establishment of an excellent product framework and steadily achieve our goals, starting with the refrigerator. Start.†Samsung will abandon its unprofitable product line and increase R&D investment for consumers in different markets.
Yin Fugen said that despite the global economic downturn leading to the stagnation of the TV market, Samsung still plans to sell 55 million flat-panel TVs this year, up from 51 million last year. Samsung expects large-screen televisions larger than 65 inches will lead the growth of the entire industry, the company has just released three ultra-high-definition television. Analysts expect Samsung’s home appliance business to realize revenue of 13 trillion won (approximately US$12 billion) last year.
Samsung also announced that it plans to invest 1.2 trillion won in the medical device business by 2020, pushing its annual revenue to reach 10 billion U.S. dollars. Samsung's medical equipment sales this year will grow from 300 million U.S. dollars last year to 500 million U.S. dollars. After acquiring NMR and CT scanner manufacturers, this performance will continue to grow. Samsung Electronics plans to become a global leader in the medical device industry, competing with General Electric, Philips, Hitachi, Toshiba and Siemens.
Compared with large complex thin - wall castings, civil products have lower requirements on casting quality. However, for the latter, shorten the production cycle, improve the production efficiency of the problem becomes more prominent. The gelation process of common silica sol mainly depends on the dehydration and drying of silica sol, which takes longer time than the gelation of chemical hardening ethyl silicate. Ethyl silicate shell using ammonia dry each layer can be completed in 2h, and the final hardening of silica sol generally takes more than 12h, for some deep holes and other difficult to dry parts of the need for a longer time. At the same time, because the Investment Casting shell needs to be made in layers, each layer needs to be fully dried, to ensure that the lower shell immersion coating will not cause the problem of remelting off, and immersion coating itself, water will be immersed in the dried shell, resulting in a long overall drying cycle. It is a schematic diagram of the production cycle of silica sol shell investment casting under general conditions. As can be seen from the figure, shell making time accounts for more than 50% of the whole casting production cycle. To shorten the delivery time and shell making cycle is the core of the problem. The key factors to shorten the shell-making period can be divided into two aspects: internal cause and external cause. The main internal cause is the characteristics of the binder, and the external cause is the drying condition.
Silica Sol Casting industry in China is developing rapidly and its application is also very extensive.
Tianhui Machine Co.,Ltd , https://www.thcastings.com